Newswise — Artists shape clay into a new form at the potter’s wheel. When fired in the kiln, the clay solidifies and strengthens into artwork that can last thousands of years. The physical process during kiln firing is known as sintering. This process transforms particles, like a powder, into a solid object by heating it below the materials’ melting points.
Idaho National Laboratory (INL) materials researchers use an advanced version of sintering, called Electric Field Assisted Sintering (EFAS), to create materials. EFAS systems rely on rapid joule heating, which sends electricity through two large metal presses on either side of the material, and sometimes the material itself, to fuse the particles of powdered metals, ceramics or a mixture of both. This is the same mechanism as an incandescent lightbulb: electric current passes through a tungsten filament, which eventually heats enough to glow.
Like pottery, these parts are manufactured for durability. But they’re also designed to withstand harsh environments like nuclear reactors, concentrated solar plants, geothermal systems and armor. They can also be used for aerospace applications.
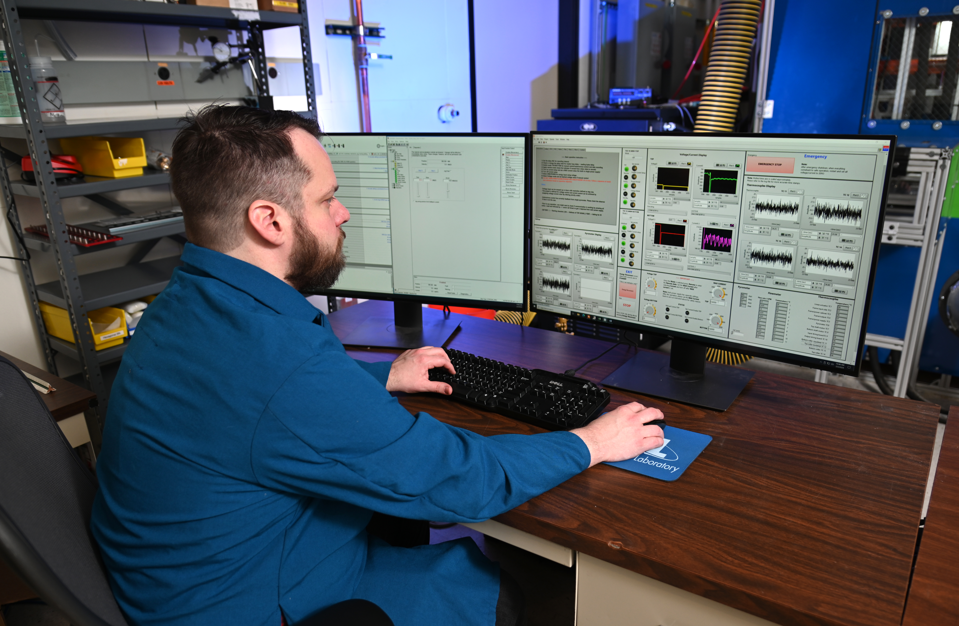
INL leads the U.S. in developing EFAS technologies to meet material requirements for next-generation energy solutions. The lab has unique capabilities ranging from probing the sintering process at the nanoscale to manufacturing parts at industrially relevant scales. In 2021, INL commissioned the DCS-800, the world’s largest EFAS platform that is available for research and development purposes.
Recently, INL researchers invented, built and commissioned a new EFAS technology, known as Continuous Electric Field Assisted Sintering (CEFAS). This project was funded by the Department of Energy’s Advanced Materials and Manufacturing Technology Office.
All EFAS instruments, including the CEFAS, sinter materials by applying pressure and heat. The CEFAS differs from other EFAS instruments because it sinters materials continuously rather than in batches. “The CEFAS is unique among all EFAS technologies as it is the only instrument capable of producing parts continuously,” said Andrew Gorman, a materials scientist leading CEFAS development. “By shifting from a batch to a continuous process, the CEFAS has the potential to increase part production by a hundred-fold compared to batch EFAS.”
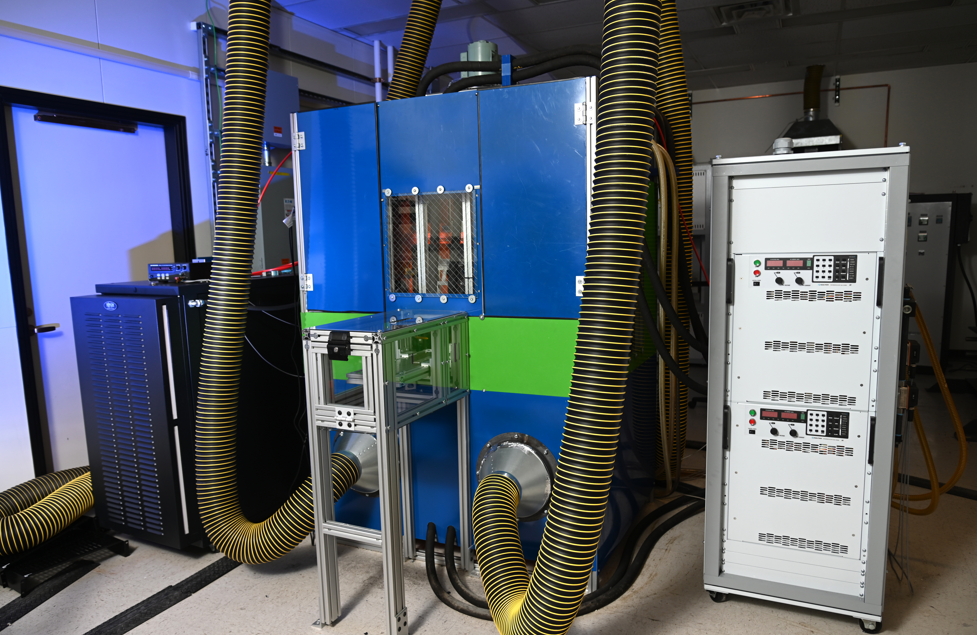
In traditional EFAS, samples are typically placed into a mold located between two giant metal presses known as rams. Electrical current passes through the rams into the mold, which heats the mold while the rams simultaneously apply pressure on the material. This squeezes the material, removing all air space and molding it into a cohesive part. In contrast, the CEFAS passes material through two rotating graphite rollers heated using the same physics leveraged in traditional EFAS, allowing for samples of unlimited length.
“The CEFAS has the potential to be a pivotal technology in advanced materials manufacturing across multiple industries,” said Gorman. “There are materials processed today that require days or weeks in a furnace. Even if it required multiple passes through the CEFAS, the cost, energy requirements and carbon emissions would be drastically reduced.”
The CEFAS has successfully reached temperatures needed to process several materials. Going forward, the CEFAS team will produce samples to demonstrate the machine’s capabilities.
“We know that the CEFAS will excel in traditional EFAS application areas, but with the unique heating profiles and continuous process, there could be new applications that we don’t yet know about,” said Gorman. “It feels like we’re just scratching the surface with the CEFAS’ potential.”
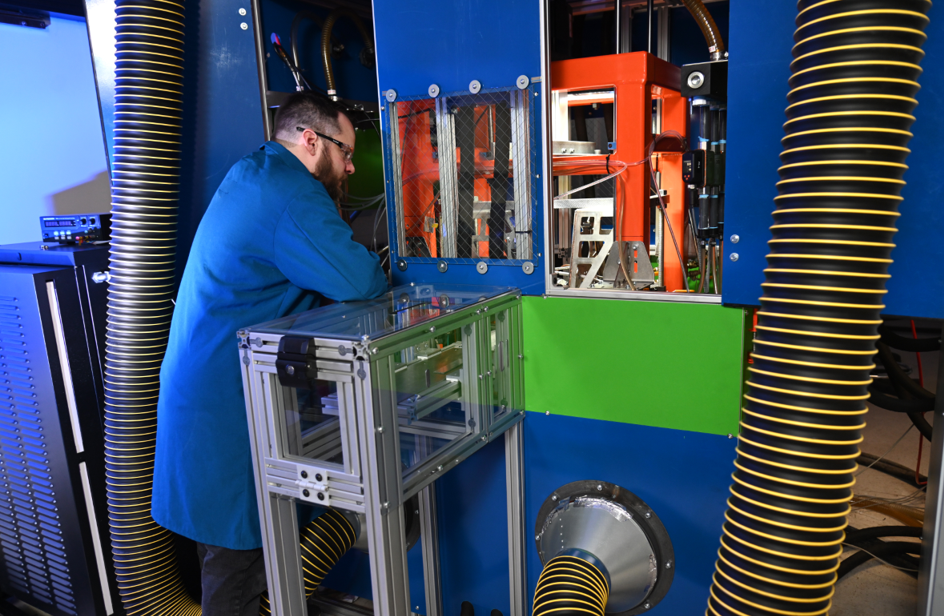