Newswise — ALBUQUERQUE, N.M. — Sal Rodriguez, a nuclear engineer at Sandia National Laboratories, is forging a rocket revolution with the help of the University of New Mexico and student Graham Monroe.
Their cutting-edge research is propelling the future of aerospace by infusing rocket science with a touch of golf ball magic.
They incorporated dimples similar to those found on golf balls, a key element in Rodriguez’s fluid dynamics and heat transfer research.
The making of the rocket nose
The idea started in 2019 when Monroe was working with Rodriguez at Sandia as a student intern.
“I was always interested in aerodynamics,” Monroe said. “I was working on my bachelor’s in engineering degree in 2019 when I took part in the Lobo Launch at the Spaceport America Cup. Meanwhile, Sal was researching some dimpling projects. We started talking and came up with the idea of dimpling the nose cone of a rocket.”
The experiment turned into Monroe’s master’s thesis project.
They started with the dimpling program that Rodriguez created starting in 2014 and copyrighted in 2017.
“The program includes a specific set of equations that allows the user to look at an object’s geometry and add the velocity and the fluid it’s traveling through,” Rodriguez said. “You put that into the program, and it outputs the required dimple pattern.”
Monroe then 3D printed the nose cone. UNM’s Lobo Launch team, meanwhile, created the accompanying rocket and a smooth nose cone that was identical, minus the dimples.
Due to the COVID-19 pandemic, and the fact that the Lobo Launch team needed their rocket for the upcoming Spaceport America Cup competition, launching the rocket became a challenge.
It was finally put to the test in November and December of 2022.
“We were overjoyed when we found that the dimpled rocket had 22 percent less frictional drag compared to a smooth rocket,” Rodriguez said. “At its peak, it reduced drag by 39.1 percent. So that’s less fuel you need, and it produces less CO2 which is good for the environment.”
Monroe successfully defended his thesis in the fall of 2023, earning the coveted “pass with distinction.”
“It’s been really neat to be part of this research,” Monroe said. “To be part of something that could be used in the real world. When we look at the day and age that we are in, as far as space exploration, the effect this could have on energy savings is really significant.”
How dimples work
So how do these dimples work?
“They generate turbulence, redistribute the turbulent energy, accelerate the flow in the dimpled regions and reduce the boundary layer thickness,” Rodriguez said.
He said a good analogy is an Olympic diving competition: “The diver who plunges into the water with the smallest splash gets extra points because only a very small amount of resultant water flow is generated by the more aerodynamic dive. The same occurs with dimples. They generate a flow pattern that is so aerodynamic, that only small, disorderly flow currents are generated by the dimpled objects — a gold medal dive.”
Bring in the Mustang
But it’s not just rockets that can benefit from this dimpling. Rodriguez has been exploring other ways to use dimples. In a little-known project with Bobby Unser Junior, he dimpled the hood of a Ford Mustang.
“It was so exciting because he was so enthused about racing and race cars,” Rodriguez said of Unser. “I told him about my copyright and that I could dimple his sports car and make it go faster. He was very excited.”
Rodriguez used his program to find the ideal size and placement of the dimples on the car’s hood. Like the rocket, the results were significant. They showed a minimum 25% reduction in airflow drag compared to a car with no dimples. The experiment also included a car with tennis ball sized dimples, to prove that while all dimpling helps, precision with dimples is key.
Whether consumers would be okay with dimples on their car was another question the pair hoped to explore. Unfortunately, Unser died before the project went any further.
It’s not just in aerodynamics
One of Rodriguez’s latest projects is using dimples in heat transfer.
With the help of funding from the New Mexico Small Business Assistance Program, he has built an apparatus that shows how dimples can speed up the heating process.
A box with three sides of plexiglass and one side of dimpled aluminum is filled with water and then connected to a heat source.
“We put beads and dye in there to see how they move along the dimples,” Rodriguez said. “We witnessed them accelerate, twice the velocity than outside the dimple area, and with increased turbulence.” That proves that the dimpling enhances heat transfer.
Rodriguez says this technology can be transformed into a solar water heater. That could be life-changing for places that don’t have easy access to electricity, such as Indian reservations or developing nations. It has already caught the attention of a company in another country.
The road ahead
Rodriguez’s dimpling work is far from done. His team recently submitted a non-provisional patent application for dimpled wind turbines.
“We can apply to rockets, aircraft, cars, electronic vehicles, submarines, drones and wind turbine blades,” Rodriguez said. “We can extend the distance that they can travel or the energy they harvest. Dimpling will have a beneficial effect on aerodynamics. We will be able to design rockets that can carry a much heavier payload in space and make space exploration more affordable by at least 10 to 20 percent.”
While his work is very practical, Rodriguez also hopes to have a little fun with it. He’s already dreaming up new ideas. “Maybe we could do speedboats, jet skis, even frisbees,” Rodriguez said.
Sandia National Laboratories is a multimission laboratory operated by National Technology and Engineering Solutions of Sandia LLC, a wholly owned subsidiary of Honeywell International Inc., for the U.S. Department of Energy’s National Nuclear Security Administration. Sandia Labs has major research and development responsibilities in nuclear deterrence, global security, defense, energy technologies and economic competitiveness, with main facilities in Albuquerque, New Mexico, and Livermore, California.
MEDIA CONTACT
Register for reporter access to contact detailsArticle Multimedia
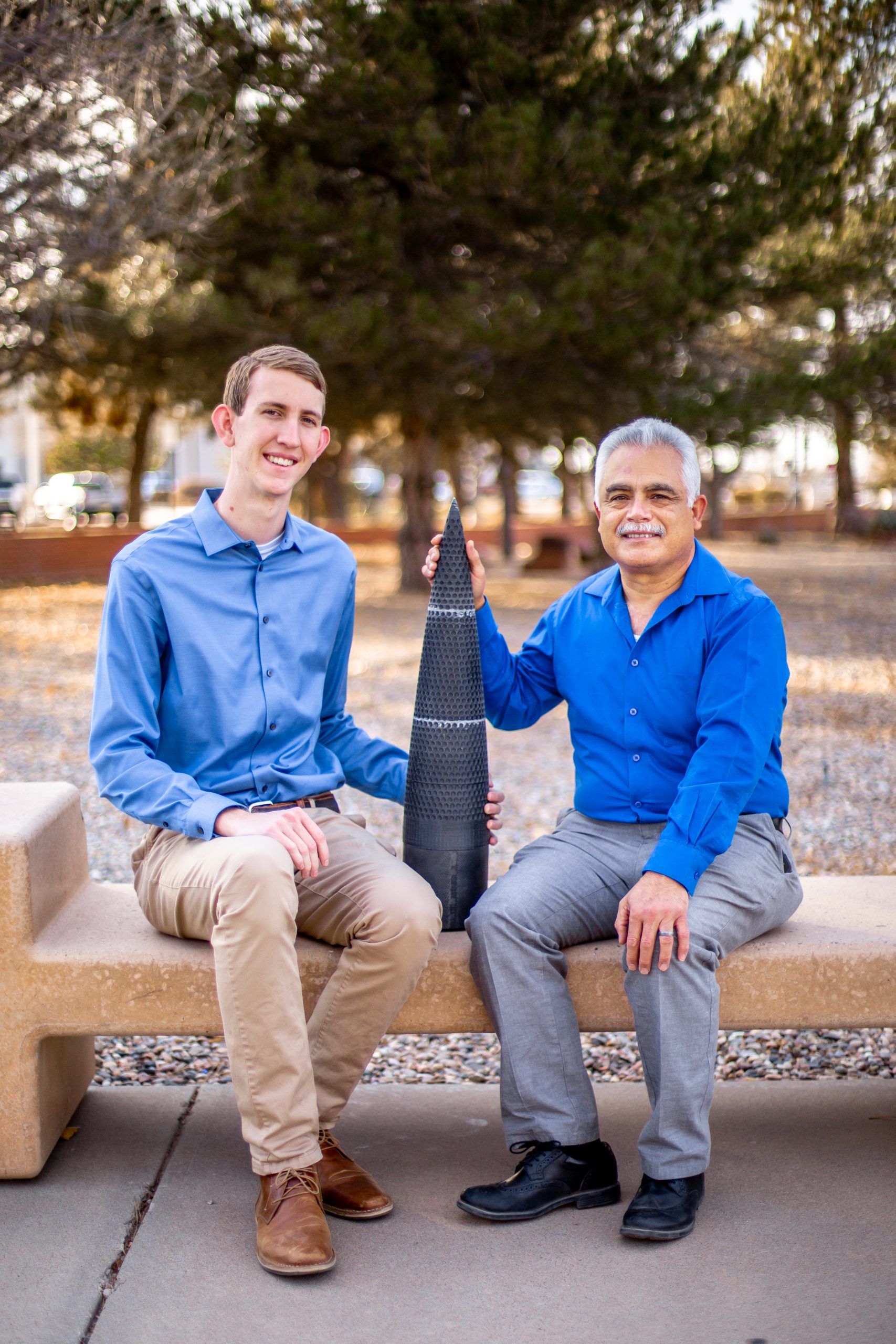
Credit: Jennifer Plante/Sandia National Laboratories
Caption: Graham Monroe, left, and Sal Rodriguez display the dimpled rocket nose they built as part of a collaboration between Sandia and the University of New Mexico.
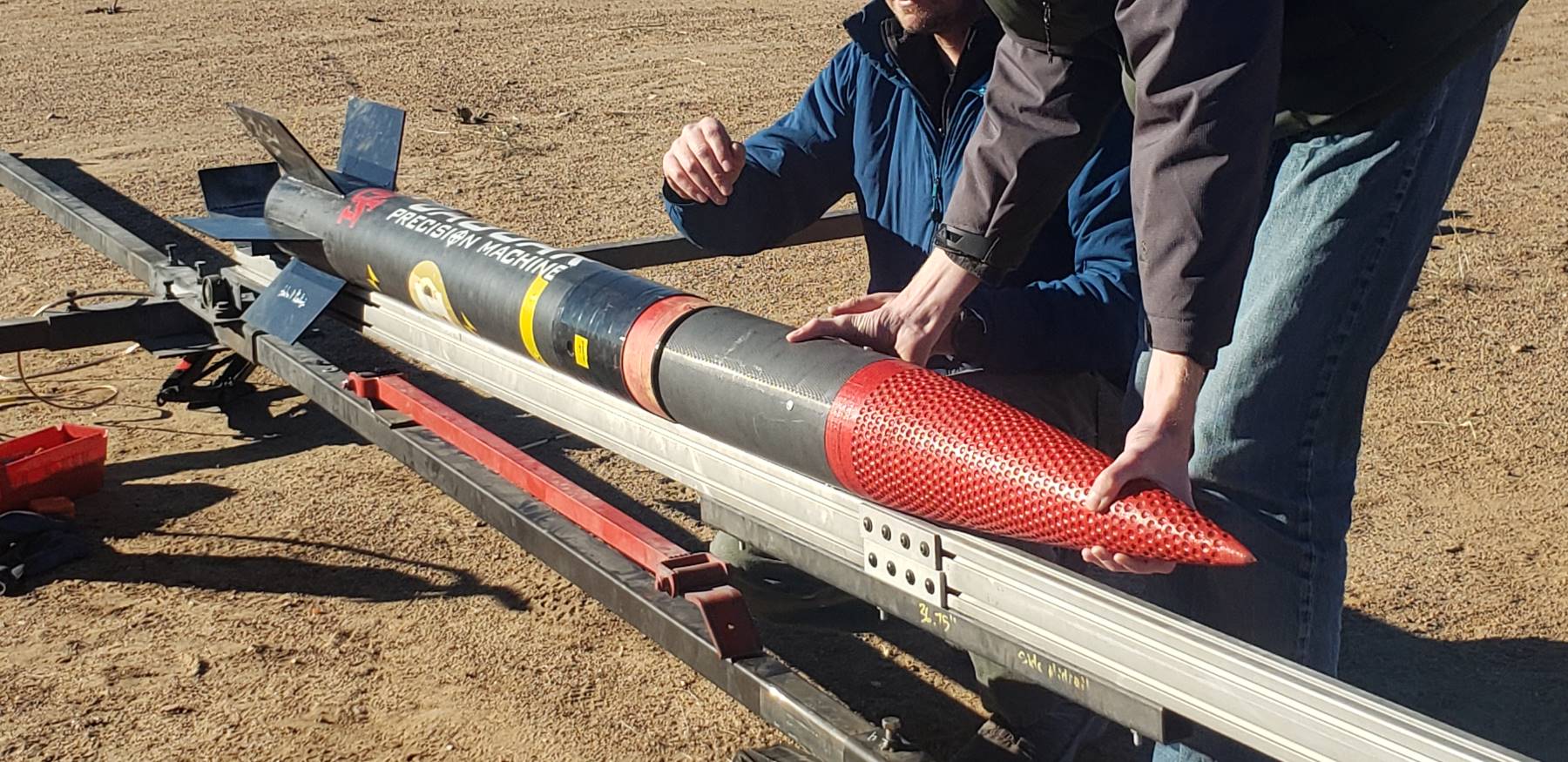
Credit: Sal Rodriguez
Caption: The dimpled rocket created by Sal Rodriguez and Graham Monroe was tested in December of 2022.
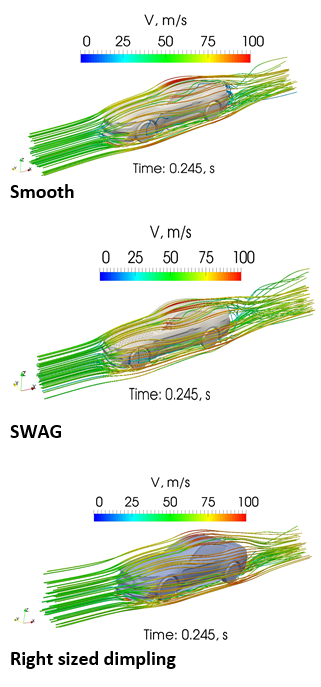
Credit: Sal Rodriguez
Caption: Computer simulation shows how dimples affect drag.
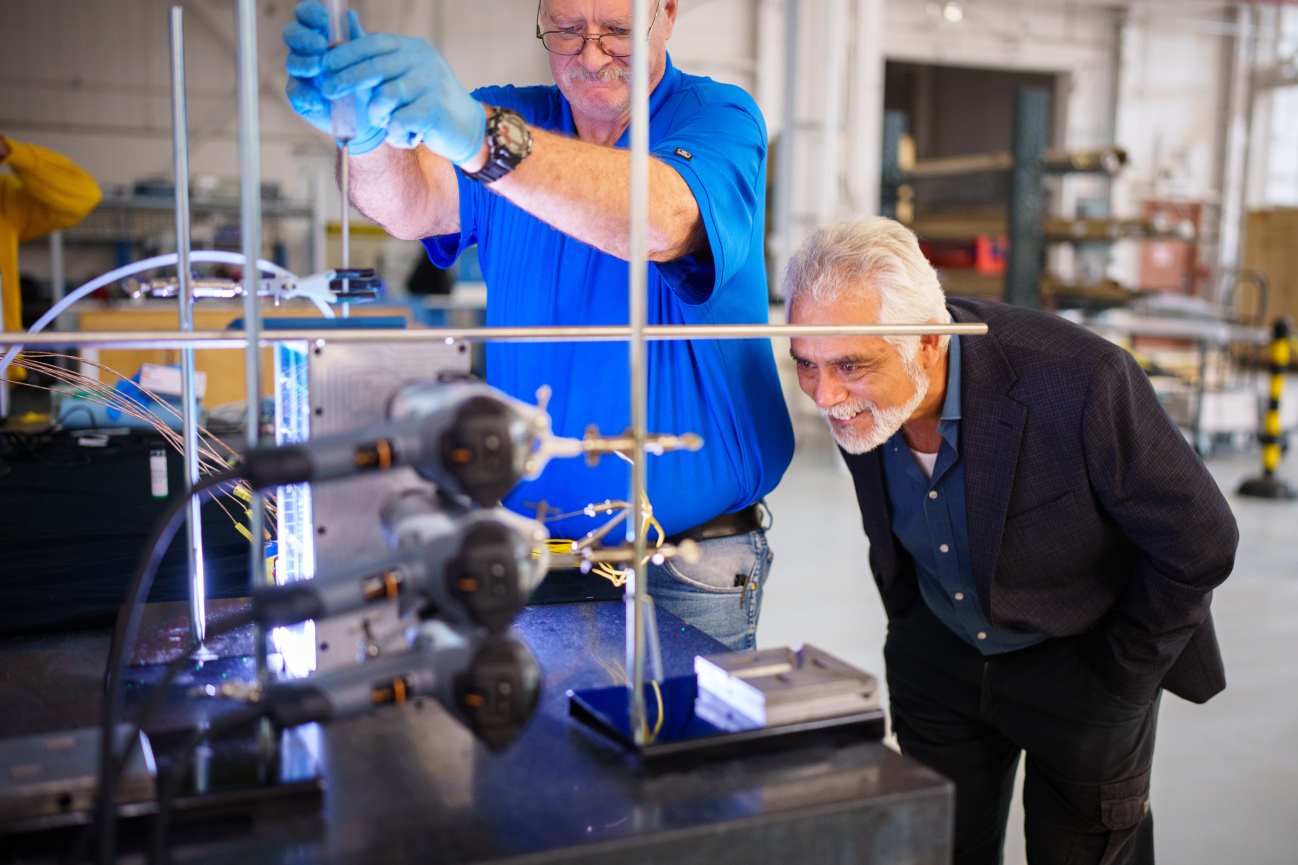
Credit: Craig Fritz
Caption: Sal Rodriguez, right, looks on in amazement as technologist Robin Sharpe injects dye into the dimpled model they built, showing the way dimples increase heat transfer in water.